Así es el reto español de fabricar grandes componentes de reactores de fusión nuclear
El proyecto Rodas desarrolla tecnologías de fabricación avanzadas para impulsar la industria de fusión nuclear española
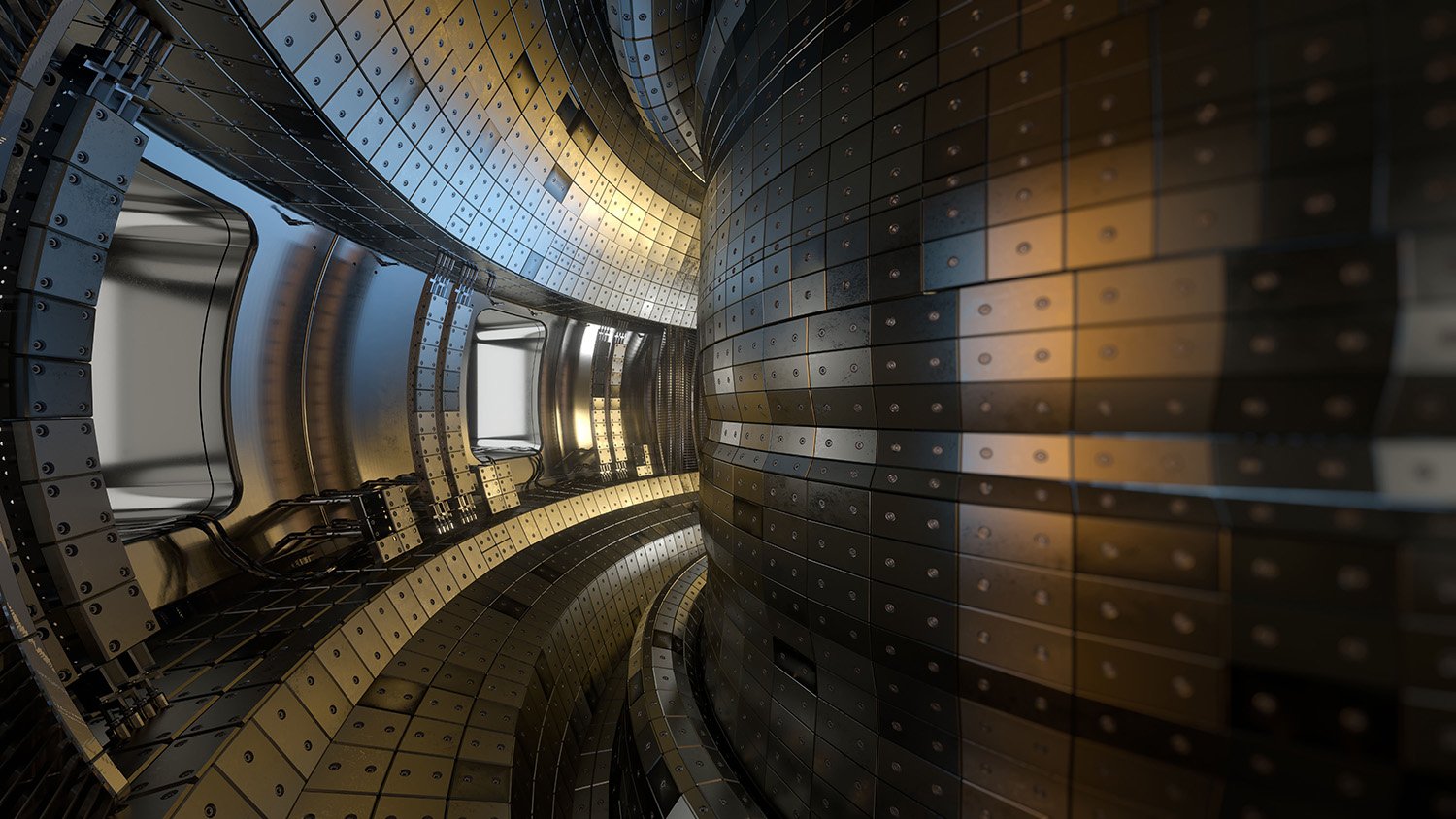
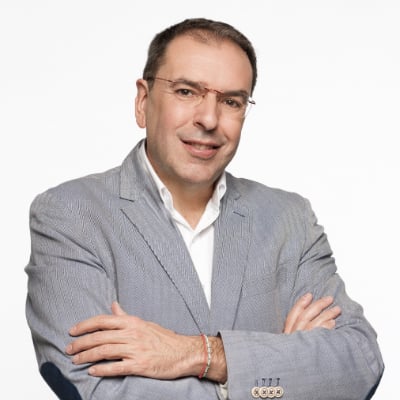
La industria asociada a la actividad nuclear se enfrenta a grandes desafíos y retos a la hora de innovar, diseñar y fabricar componentes de gran tamaño para la fusión nuclear.
Para conseguir este desafío se requiere la fabricación de componentes de gran tamaño con geometrías extremadamente complejas y excelentes propiedades mecánicas, capaces de resistir muy altas temperaturas y radiaciones, que sigue siendo el reto clave para el desarrollo de esta tecnología.
Con el objetivo de superar estas barreras, nace el proyecto Rodas, una iniciativa que busca desarrollar tecnologías de fabricación avanzada, enfocadas especialmente en el campo de la fabricación aditiva combinada con tecnologías como el prensado isostático en caliente (HIP, Hot Isostatic Pressing), para la producción de componentes críticos para los reactores de fusión nuclear.
Solución energética prometedora
Desde los impulsores del proyecto tienen claro que «la fusión nuclear se presenta como una de las soluciones energéticas más prometedoras para el futuro, gracias a su seguridad y a la disponibilidad prácticamente inagotable de recursos».
Este proyecto, con una duración de cuatro años, «pretende dotar a las empresas de conocimientos y tecnología, que les permita afrontar futuros proyectos en el campo de la fusión nuclear en España», añaden.
Rodas tiene presupuestado 7,78 millones de euros para alcanzar este fin contando con una financiación pública de 5,54 millones de euros procedentes Ministerio de Ciencia, Innovación y Universidades a través del Centro para el Desarrollo Tecnológico y la Innovación (CDTI) y de la Agencia Estatal de Investigación (AEI), en el marco de la iniciativa TransMisiones 2024.
El objetivo es el ayudar a resolver los retos actuales que existen para obtener los componentes de reactores de fusión nuclear. Entre ellos se encuentran cómo afrontar los largos plazos de entrega, los complejos procesos de fabricación que involucran multitud de etapas sucesivas de mecanizados, uniones y tratamientos térmicos, así como los elevados consumos de materias primas y energía.
Innovación en materiales, tecnologías de fabricación y ensayos
El proyecto se presenta articulado en torno a tres áreas clave: materiales y tecnologías de fabricación y ensayos avanzados. «Con los resultados obtenidos se capacitará a las empresas en conocimientos y tecnología para abordar futuros proyectos y licitaciones relacionadas con la fusión nuclear», indica Nerea Ordás, directora de Fabricación Aditiva de CEIT.
En el ámbito de los materiales avanzados, y aquí aparece la jerga especializada del sector, «se trabajará en el desarrollo de nuevas aleaciones pulvimetalúrgicas, como EUROFER y CuCrZr, capaces de soportar altas temperaturas y radiación».
Además, apuntan que se optimizará el proceso de atomización con gas para mejorar la producción de polvos metálicos empleados en fabricación aditiva, facilitando así su integración en los procesos industriales.
Nuevas aleaciones de alto rendimiento
En este sentido, se trabajará en la investigación y el desarrollo de nuevas aleaciones de materiales de alto rendimiento y propiedades termomecánicas avanzadas especialmente diseñadas para componentes de fusión nuclear.
El objetivo es demostrar que «la tecnología de fabricación aditiva es técnica y económicamente viable para obtener componentes refrigerados activamente, de geometría compleja y grandes dimensiones, capaces de cumplir con los estrictos requerimientos de la fusión nuclear», señala Marcos Pérez, director de desarrollo de negocio de Leading Metalmechanical Solutions.
En cuanto a la fabricación avanzada, se investigarán diferentes técnicas de fabricación a partir de polvo o hilo metálico, como PBF-L (Fusión Directa de Metal por Láser), DED (Deposición de Energía Focalizada), WAAM (Fabricación Aditiva mediante arco e hilo) o la novedosa técnica ROV-MAM, con el objetivo de obtener piezas con geometrías complejas y de grandes dimensiones y consiguiendo a su vez una reducción significativa del desperdicio de material. Además, se investigará también la hibridación de procesos de fabricación.
Prensado Isostático en Caliente
Una de las principales innovaciones del proyecto Rodas va a ser la posibilidad de aplicación simultánea de tratamientos térmicos y la tecnología de Prensado Isostático en Caliente (HIP, Hot Isostatic Pressing) desarrollada por Hiperbaric.
«Estamos desarrollando una nueva generación de prensa y horno de HIP de grandes dimensiones, único en España, con altas velocidades de enfriamiento y dotada con una arquitectura avanzada de control mediante la aplicación de inteligencia artificial», indica Andrés Hernando, consejero delegado de Hiperbaric.
Finalmente, se realizarán ensayos avanzados para validar los nuevos materiales y procesos mediante técnicas no destructivas, como tomografía computarizada y ultrasonidos, asegurando así la integridad de los componentes sin necesidad de realizar pruebas destructivas.
Reducción de materiales
El desarrollo de estas tecnologías tendrá un impacto significativo en la industria, la ciencia y la sostenibilidad, contribuyendo al desarrollo de la fusión nuclear como fuente de energía.
Gracias a la optimización de procesos de fabricación avanzada, se espera reducir los tiempos de producción de componentes clave de ocho a dos semanas y minimizar el desperdicio de material en hasta un 80%, respetando así el medio ambiente. Además, el uso de los nuevos materiales permitirá mejorar la duración y eficiencia de los reactores de fusión.
Efecto tractor del tejido industrial español
Se generará un efecto tractor del tejido industrial español, fomentando la capacitación de las empresas en áreas temáticas relacionadas con materiales con propiedades avanzadas y permitiendo a estas compañías posicionarse en el sector de industria de la ciencia.
También facilitará el acceso a licitaciones públicas de IFMIF-DONES (Instalación Internacional de Irradiación de Materiales de Fusión – Fuente de Neutrones DEMO orientada a la demostración) o ITER (Reactor Termonuclear Experimental Internacional).
Consorcio de referencia para un proyecto ambicioso
El proyecto Rodas cuenta con un consorcio formado por dos agrupaciones. Por un lado, la agrupación del Centro para el Desarrollo Tecnológico y la Innovación CDTI, liderada por Leading Metalmechanical Solutions y compuesta por las empresas Hiperbaric, Rovalma, Innomaq21 y Novadep NDT Systems.
Por otro lado, la agrupación de la Agencia Estatal de Investigación (AEI), encabezada por la Asociación Centro Tecnológico CEIT y formada por CIEMAT, Fundación IDONIAL y la Universidad de Granada.
Mientras que la agrupación AEI asumirá la investigación, el desarrollo de materiales, la optimización de procesos de fabricación y la validación de componentes, la agrupación CDTI se centrará en la validación de tecnologías de fabricación avanzada y desarrollo de aplicaciones a escala real.
Investigación y experiencia
Esta combinación de conocimiento investigador y experiencia práctica industrial garantiza la viabilidad y el éxito del proyecto, permitiendo la transferencia efectiva de los avances científicos a la industria.
El proyecto se puso en marcha el pasado mes de enero con una reunión celebrada en las instalaciones de Ceit, en la que participaron todos los socios del consorcio. Durante el encuentro se definieron los primeros pasos y se estableció la hoja de ruta para los próximos años.
Iniciativa de la Universidad de Navarra
Ceit es un centro tecnológico integrado en el Basque Research and Technology Alliance (BRTA), y creado en 1982 por iniciativa de la Universidad de Navarra. Como organización privada sin ánimo de lucro, su misión es mejorar la competitividad de las empresas mediante la generación y transferencia de conocimiento en el ámbito de la investigación aplicada.
Con una fuerte orientación a la industria, Ceit trabaja en estrecha colaboración con empresas de diversos sectores para desarrollar soluciones tecnológicas innovadoras que respondan a sus necesidades estratégicas. Su especialización se articula en torno a tres grandes áreas: fabricación avanzada, movilidad sostenible y economía circular.
Empresas participantes
Leading es una PYME constituida en 1972 y centrada en el diseño, desarrollo y fabricación de mecanizados y soldaduras de precisión, prototipos, producción en serie corta-media de componentes, así como de utillajes y modelos, en una amplia gama de materiales, tanto férricos como no férricos, y en todo tipo de formas productivas.
El negocio principal de esta empresa es, por lo tanto, el mecanizado y la soldadura de precisión; la entrega de conjuntos mecánicos complejos, ofreciendo la posibilidad de una gestión completa de los procesos mediante el suministro de proyectos llave en mano.
Se centra en obtener la mejor solución de diseño para mejorar el desempeño del producto basándose en las especificaciones y requerimientos iniciales del cliente, trabajando de cerca con cada cliente, entregando el producto terminado con todas las certificaciones requeridas.
Maquinaria de altas presiones
Hiperbaric es una empresa burgalesa dedicada, desde el año 1999, al diseño, fabricación y comercialización de tecnología y equipos industriales de altas presiones. Desde hace más de dos décadas es proveedora de maquinaria para el Procesado por Altas Presiones (High Pressure Processing, HPP) aplicada al sector alimentario, en la que es líder mundial con más del 65% de la cuota de mercado.
En 2019 abrió una nueva línea de negocio centrada en el diseño y desarrollo equipos industriales para el Prensado Isostático en Caliente (Hot Isostatic Pressing, HIP).
En 2021 pone en marcha otra innovadora línea de negocio: la tecnología de Compresión de Hidrógeno (H2) a muy alta presión, proveniente de energías renovables, para participar en el reto de la movilidad sostenible y la descarbonización de la industria. En 2024 la compañía celebró su 25 aniversario.